在全球汽車行業電動化轉型的大背景下,電動汽車(EV)的普及速度日益加快。隨著用戶對電動汽車續航里程和充電速度需求的不斷提升,車載充電器(OBC)作為電動汽車的關鍵部件,其性能提升和設計改進顯得尤為重要。為了滿足更高的功率等級和電壓要求,OBC 設計正經歷著一系列深刻變革。
一、OBC 的重要性及發展背景
OBC 的主要功能是將交流電轉換為直流電,從而為電動汽車的電池充電。在當前的充電基礎設施中,雖然直流快充技術發展迅速,但交流充電憑借其廣泛的分布和較低的成本,依然是電動汽車充電的重要方式。這使得 OBC 在電動汽車領域不可或缺。
早期電動汽車的 OBC 功率普遍較低,一般在 3.6kW 以下,難以滿足如今大容量電池的快速充電需求。同時,隨著電動汽車技術的發展,電池電壓逐漸從傳統的 400V 向 800V 甚至更高電壓平臺邁進。這不僅是為了提高電池的能量密度和續航能力,還能有效降低電流,減少傳輸過程中的能量損耗。例如,在一些高端電動汽車中,800V 電池架構已開始應用,這就要求 OBC 必須具備更高的電壓轉換能力和功率處理能力。
二、OBC 面臨的新需求
(一)更高的功率等級
隨著電動汽車電池容量的不斷增大,如從早期的幾十千瓦時發展到如今部分車型超過 100 千瓦時,若繼續使用低功率的 OBC 進行充電,充電時間將變得難以接受。以一款 100 千瓦時電池容量的電動汽車為例,使用 7kW 的 OBC 充電,理論上充滿電需要超過 14 小時。因此,為了縮短充電時間,行業開始向更高功率等級的 OBC 發展,目標功率范圍逐漸提升至 11kW 至 22kW 甚至更高。
(二)適應高電壓平臺
隨著 800V 電池架構的逐漸普及,OBC 需要對其進行適配。在傳統 400V 系統中,OBC 使用的 650V 額定電壓的功率器件和芯片,無法直接應用到 800V 架構中。因為更高的電壓對器件的耐壓能力提出了更高要求,需要采用擊穿電壓更高的元件,例如將標準的 650V 額定芯片元件過渡到額定電壓最高達 1200V 的芯片元件。
三、OBC 設計改進的挑戰
(一)散熱管理
隨著功率等級的提升,OBC 在工作過程中產生的熱量大幅增加。以從 7kW 提升到 22kW 功率為例,發熱量可能會增加數倍。而電動汽車內部空間有限,難以容納過大的散熱裝置。如果不能有效解決散熱問題,過高的溫度將影響 OBC 中電子元件的性能和壽命,甚至導致系統故障。例如,功率半導體如 SiC MOSFET 的散熱依賴于熱界面材料(TIM)的均勻壓縮,但在實際應用中,PCB 翹曲、冷卻板變形和 TIM 不均勻壓縮等問題,可能導致局部過熱。
(二)封裝限制
更高的功率等級和電壓要求,意味著 OBC 需要集成更多高性能的電子元件,這對其封裝設計提出了挑戰。一方面,要在有限的空間內合理布局這些元件,確保電氣連接可靠、信號傳輸穩定;另一方面,封裝材料需要具備更高的絕緣性能和散熱性能,以適應高電壓和高功率帶來的影響。
(三)器件成本
采用更高耐壓和性能的元件,如 1200V 的芯片元件,以及高性能的碳化硅(SiC)元件等,往往會增加器件成本。而在電動汽車市場競爭激烈的情況下,控制 OBC 的成本對于整車成本控制至關重要。如何在保證性能的前提下,降低器件成本,是 OBC 設計改進需要解決的問題。
(四)電磁兼容性(EMC)
OBC 在工作過程中會產生電磁干擾,尤其是在高功率和高電壓條件下,電磁干擾問題可能更加嚴重。如果不能有效解決 EMC 問題,不僅會影響 OBC 自身的正常工作,還可能對電動汽車上的其他電子設備產生干擾,影響整車的安全性和可靠性。
(五)安全問題
更高電壓的系統需要更強的絕緣和安全功能。在設計 OBC 時,必須確保在高電壓下,系統不會對人員和車輛造成安全隱患。同時,對于高電壓系統的測試和驗證也更為復雜,需要專門的設備和專業知識,以確保系統的安全性和可靠性。
四、OBC 設計改進的方向與策略
(一)采用新型半導體材料
在應對高電壓和高功率挑戰方面,碳化硅(SiC)等新型半導體材料展現出明顯優勢。與傳統硅材料相比,SiC 具有更高的擊穿電場強度、更高的熱導率和更低的導通電阻。在需要更快 MOSFET 開關的更高電壓應用(例如 OBC)中,改用 SiC 元件可以有效降低導通損耗和開關損耗,提高充電效率。例如,英飛凌在其 OBC 技術路線圖中提到,支持三相交流電網輸入和 800V 電池電壓的 OBC 可以采用 1200V SiC MOSFET,配合帶 CLLC DC/DC 諧振轉換器的三相 PFC,能夠實現更高的功率密度和更優的性能。
(二)優化電路拓撲結構
通過采用先進的電路拓撲結構,可以提高 OBC 的功率轉換效率和性能。例如,多端口串聯諧振拓撲等技術能夠優化電能轉換過程,減少能量損失。同時,在設計電路拓撲時,充分考慮功率因數校正(PFC)功能,調整電壓和電流相位,最大限度地減少對交流電網的影響。對于雙向 OBC,還需要設計合適的拓撲結構,以實現電池與電網之間的雙向能量傳輸。
(三)創新散熱技術
為了解決散熱難題,可采用雙面冷卻技術、微通道冷卻技術等創新散熱技術。雙面冷卻技術能夠大幅降低功率器件的峰值溫度,提高系統效率。微通道冷卻技術則通過在冷卻板中設計微小的通道,增加冷卻液與發熱元件的接觸面積,提高散熱效率。此外,合理設計冷卻系統的布局,確保冷卻液均勻分布,避免出現熱熱點。同時,在器件布局上,將發熱量大的組件靠近散熱系統,并預留足夠的空間用于空氣流通或冷卻液通道。
(四)集成化與模塊化設計
采用集成化與模塊化設計理念,將多個功能模塊集成在一起,可以減少 OBC 的體積和重量,提高功率密度。例如,安森美的 APM32 功率模塊系列集成了先進的 1200V SiC 器件,針對 800V 電池架構進行了優化,適用于高電壓和功率級 OBC。該系列模塊包括用于功率因數校正(PFC)級的三相橋模塊,相較于分立方案,具有尺寸更小、散熱設計更佳、雜散電感更低、內部鍵合電阻更低、電流能力更強、EMC 性能更好、可靠性更高等優勢,有助于創建高性能雙向 OBC。
(五)提升電磁兼容性設計
在 OBC 設計過程中,從電路布局、屏蔽設計、濾波電路等多個方面入手,提升電磁兼容性。合理布局電路,減少信號之間的干擾;采用屏蔽材料對敏感元件進行屏蔽,防止電磁干擾的傳播;設計合適的濾波電路,濾除高頻干擾信號。同時,在產品研發階段,通過嚴格的 EMC 測試,對設計進行優化和改進,確保 OBC 滿足相關的電磁兼容性標準。
五、結語
隨著電動汽車技術的不斷發展,對 OBC 的功率等級和電壓適應性提出了更高要求。通過不斷改進 OBC 設計,采用新型半導體材料、優化電路拓撲結構、創新散熱技術、進行集成化與模塊化設計以及提升電磁兼容性設計等策略,可以有效應對這些挑戰,提升 OBC 的性能和可靠性。這不僅能夠滿足消費者對電動汽車充電速度和便捷性的需求,還將推動電動汽車行業的進一步發展,為實現綠色出行目標提供有力支持。在未來,隨著技術的持續進步,OBC 設計有望取得更多突破,為電動汽車的廣泛普及奠定堅實基礎。
上一篇:利用隔離放大器應對電動汽車中精確電壓檢測的挑戰
下一篇:最后一頁
推薦閱讀最新更新時間:2025-05-22 15:35
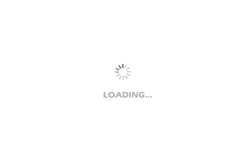
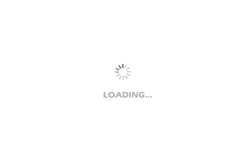
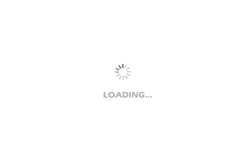
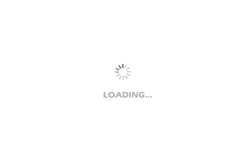
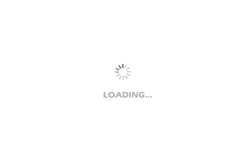
- MCP3905EV,用于計量客戶的 MCP3905 電能計量 IC 的評估板
- AS3930 演示系統,AS3930 喚醒接收器的演示板包括一維喚醒模式檢測、虛假喚醒讀出
- 使用 ROHM Semiconductor 的 BD45291 的參考設計
- ONS321A5VGEVB:5 Vgs MOSFET 評估板
- 2022電子設計競賽省賽F題跟隨小車設計
- LTC2635-LMX10 四通道、10 位數模轉換器的典型應用
- NCP5104SYNCBUCKGEVB:可變直流輸入、開環同步降壓評估板
- 用LED替代低效率的MR16鹵素燈
- DC2296A DC2209和DC2210數字溫度測量系統
- 【訓練營】一條狗腿子