在現代電動汽車(EV)和混合動力電動汽車(HEV)中,電池管理系統(BMS)堪稱電池組的核心大腦,其承擔著確保電池性能優良、運行安全以及壽命長久的重任。BMS 對諸多關鍵參數,如充電狀態(SOC)和健康狀態(SOH)進行精準跟蹤。SOC 清晰地反映出電池內可用能量的情況,而 SOH 則用于全面評估電池單元的整體狀況以及老化程度。通過密切監控這些關鍵指標,不僅能夠實現高效的能源利用,還能有效預防電池過早出現退化現象。
為契合電池效率和環境可持續性方面的法規要求,汽車制造商必須全力以赴,在車輛的整個生命周期內維持較高水平的電池健康狀態。舉例來說,加州空氣資源委員會制定了相關標準,明確規定到 2030 年車型年,電動汽車務必在 10 年時間或者行駛 150,000 英里的里程內,至少保持 80% 的電動續航里程。類似的標準在全球范圍內紛紛生效實施,這就迫切要求在 BMS 中采用更高的電池電壓以及更為先進的傳感技術,以此來提升檢測精度。本文將深入探討與分立電阻鏈相比,集成高壓電阻分壓器如何提供一種更精確且更節省空間的電壓衰減方法,進而助力 BMS 更好地平衡電池包并延長其使用壽命。
電動汽車電池系統現狀與挑戰
典型的電動汽車電池電壓通常大于等于 400V,并且當前行業正朝著 1kV 甚至更高電壓的方向發展。這一趨勢背后的主要原因在于,輸出功率更大的 EV 電池充電器能夠顯著加快車輛的充電速度,因為功率(P)等于電流(I)與電壓(V)的乘積,即 P = IV。為達到特定的充電速度,可利用這一電壓 / 電流關系,通過提升電壓,在保持電流值最小化或者維持平穩的同時,依舊能夠提供所需的功率。在 EV 設計中,將電流值降至最低具有重要意義,因為熱量會對電池和電子元件的使用壽命產生負面影響,而電流增加會導致電動動力總成內的散熱大幅增加。此外,電流的減少使得使用更輕規格的電線成為可能,這不僅減輕了整體線束的重量,還能讓車輛在相同電量下行駛更遠的距離。
直接對電池電壓進行測量,并將其傳輸至相關的數字車輛系統時,需要借助模數轉換器(ADC)來進行信號轉換,而 ADC 一般由 5V 左右的電壓供電。由于輸入信號若超過 5V 極有可能損壞 ADC,因此,為保護 ADC 和其他低壓元件免受電池相對較高電壓的影響,必須使用諸如隔離式放大器等器件,在高壓域和低壓域之間構建起一道安全屏障。盡管隔離式放大器能夠在兩個電壓域之間起到連接作用,但它所能接受的電壓范圍與 ADC 相近,所以在信號到達隔離式放大器之前,需要先對電池電壓進行衰減處理。通常情況下,會采用電阻分壓器來實現這一目的,將高壓信號降低至較低電壓的滿量程范圍之內。
當處理大于 400V 的電壓時,爬電距離和電氣間隙成為必須重點考慮的因素,以避免出現電弧現象,并確保實現安全絕緣。雖然傳統的電阻分壓器僅需兩個電阻,但在涉及爬電距離和電氣間隙的高壓衰減應用中,通常會采用長電阻鏈的形式,以此來增加高壓節點和低壓節點之間的物理距離。根據國際電工委員會(IEC)60115 - 8 的規定,每個電阻器的最大持續壓降是有限的。一般而言,每個 1206 外殼尺寸的表面貼裝電阻器為 200V,每個 0805 外殼尺寸的電阻器為 150V。鑒于電池電壓在高于或低于其額定值時均會發生變化,為確保安全,往往會使用過多的電阻器,這通常會導致形成由 10 個或更多分立電阻器組成的電阻鏈。
即便使用精密電阻器,每個分立電阻器固有的容差變化仍可能致使分壓比出現顯著差異,最終造成電壓測量不準確。而且,這些電阻器兩端的焊接點處于暴露狀態,這可能會引發額外的泄漏以及寄生電容或電感等問題,除非采取保形涂層或其他保護措施,但這樣又會增加解決方案的成本。在長鏈分立電阻器中,上述這些不利影響會進一步加劇,隨著時間的推移,會進一步降低電壓檢測的精度。這極有可能導致 SOC 和 SOH 的估計出現錯誤,進而引發欠佳的電池管理決策,比如不正確的充電和放電周期,最終結果便是縮短電池壽命,并削弱電動汽車的續航里程。
集成電阻分壓器的工作原理與優勢
利用現代半導體制造工藝技術,能夠在標準硅襯底晶圓上構建起薄膜硅鉻電阻層。該電阻層由二氧化硅絕緣層封裝保護,可在超過 1kV 的極高電壓環境下正常使用。將此晶圓的單個部分(即晶片)封裝到標準塑料集成電路(IC)外殼中,能夠有效保護晶片免受外部應力的影響。由于爬電距離和間隙是在引腳之間的間隙上進行測量的,所以制造商可依據設計規格,將類似尺寸的芯片封裝到更小的封裝中,以提升產品性能;或者封裝到更大的封裝中,來增加引腳之間的距離。
這種設計方法在性能和可靠性方面展現出諸多顯著優勢。因為每個晶圓部分(即芯片)的相對電阻能夠實現非常緊密的匹配,通過對初始比率以及隨時間變化的容差指定最大限值,有助于確保分壓比始終保持準確,即便受到老化或者環境變化(例如溫度變化)等因素的影響,也能維持穩定。以德州儀器(TI)的 RES60A - Q1 電阻分壓器為例,它在 10 年使用壽命內規定了 ±0.2% 的最大壽命比,這種高可靠性對于那些對性能一致性要求較高的應用而言,具有至關重要的意義。
IC 封裝設計摒棄了冗長的分立電阻器鏈,從而大幅減少了所需的印刷電路板占用空間。這種高度集成不僅極大地簡化了電路布局,還顯著降低了與元件數量相關的組裝成本。同時,更少的暴露節點降低了因泄漏或寄生效應而出錯的可能性,并且無需使用保形涂層,這在一定程度上也降低了成本。
具有差分輸出的隔離式放大器,如德州儀器的 AMC1311B - Q1,因其差分輸出在長距離傳輸信號時能夠很好地保持性能,且出于安全考慮,設計人員通常會將低壓元件放置在遠離高壓源的位置,所以這類放大器在實際應用中頗受歡迎。若要將此信號饋入單端 ADC,則需要通過添加集成差動放大器,或者圍繞放大器配置四個分立電阻器作為兩個電阻分壓器,來實現差分至單端的轉換。由同一芯片上的兩個電阻分壓器組成的集成電阻網絡同樣可以安裝在塑料 IC 封裝中,這不僅提供了應力保護,還能確保兩個分頻器之間的比率具有嚴格的公差。當與高精度放大器配合使用時,具有匹配比率的分頻器能夠產生具有極高共模抑制比的差動放大器,這對于降低噪聲和減少其他誤差具有顯著作用。
集成電阻分壓器提升電池系統性能的具體體現
在為 BMS 設計高壓衰減電路時,從傳統的分立電阻鏈過渡到采用集成電阻分壓器等集成解決方案,具有眾多不可忽視的優勢。當與用于差分信號轉換的互補集成組件,如 RES11A - Q1 等結合使用時,這些集成器件能夠助力實現具有更高電壓的電動動力系統,并且能夠提供更為準確的 SOC 和 SOH 讀數。最終的結果便是使 EV 能夠在較長時間內保持良好的電池健康狀態,從而顯著提升電動汽車的整體性能和用戶體驗。
例如,在一些實際應用場景中,采用集成電阻分壓器的電動汽車電池系統,在經過長時間的使用后,依然能夠保持較高的電池容量保持率。通過精確的電壓檢測和 SOC、SOH 估算,BMS 能夠更加合理地控制電池的充放電過程,避免過度充電或過度放電等對電池造成損害的情況發生。這不僅延長了電池的使用壽命,減少了電池更換的頻率和成本,還有效提升了電動汽車的續航里程穩定性,增強了用戶對電動汽車的信心。
此外,集成電阻分壓器的應用還為電動汽車電池系統的進一步優化和創新提供了更廣闊的空間。隨著技術的不斷發展和進步,未來可以在此基礎上進一步集成更多的功能模塊,實現對電池系統的全方位、智能化管理,推動電動汽車技術朝著更加高效、可靠、安全的方向持續發展。
上一篇:汽車4G視頻監控管理系統:安全與效率的雙重保障
下一篇:最后一頁
推薦閱讀最新更新時間:2025-05-22 16:22
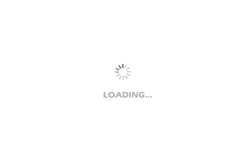
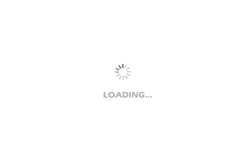
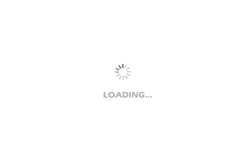
- 青柚工作室PCB尺_NFC版
- AVR602,使用 ATtinyX3U 的應用電路
- RS232 to USB
- NCP1094GEVB:PoE-PD 接口控制器評估板
- 使用 Analog Devices 的 LTC1439IG 的參考設計
- AD8188-EVALZ,用于 350 MHz 單電源三路 2:1 多路復用器的評估板
- 基于A6986H的38 V,2 A同步降壓型開關穩壓器評估板
- AD9265-125EBZ 16 位 125 Msps 評估板(兼容 HSC-ADC-EVALCZ)
- LTC2946CMS-1 雙電源、電荷和能量監視器的典型應用,使用單個光耦合器進行電流隔離,并在任一電源出現故障時使用阻塞二極管來保持數據
- 基于ESP32-WROOM-32D(16MB)的開發板設計